Precision injection molding machines play a pivotal role in modern manufacturing, especially in industries demanding high-precision plastic products. Key parameters, including injection volume, pressure, speed, and temperature control, significantly impact product quality, precision, and production efficiency. Understanding these parameters is essential for optimizing processes, improving product quality, and selecting appropriate machines.
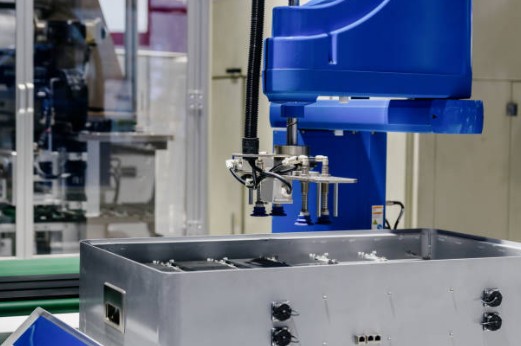
I. Injection Volume
Theoretical vs. Actual Injection Volume: Theoretical volume depends on screw diameter and stroke, while the actual volume is lower due to melt backflow and plasticizing needs. An injection coefficient (0.75 - 0.85) adjusts the theoretical value, influenced by factors like screw structure and material properties. Inconsistent actual volume leads to weight variations in products, affecting performance.
Repeatability of Injection Volume: This metric measures the consistency of injection volume. For instance, ±0.5% repeatability means the deviation from the set value is within this range. High repeatability is crucial for high-precision products; poor repeatability causes size fluctuations, impacting assembly and quality.
II. Injection Pressure
Function and Influencing Factors: Injection pressure overcomes melt flow resistance, filling and packing the cavity. It is affected by melt index, material/mold temperature, injection speed, and product design. Thin-walled products usually require higher pressure.
Pressure Requirements for Different Plastics: Low-viscosity plastics need 35 - 55MPa; medium-viscosity ones, 100 - 140MPa; high-viscosity engineering plastics, 140 - 170MPa; and micro-precision parts may need 230 - 250MPa. Incorrect pressure settings result in flash, short shots, or product deformation.
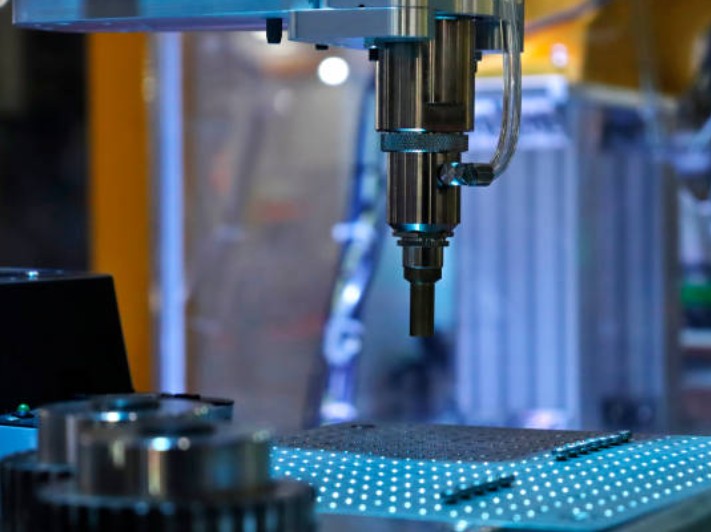
III. Injection Speed
Impact on Product Quality: A slow speed prolongs filling time, causing weld lines and uneven density, while a high speed reduces filling time but may lead to material degradation due to excessive shear. High speed is often required for thin-walled products.
Multi-stage Speed Control: Modern machines use multi-stage control: low speed at the start to protect the mold, increased speed for filling, and reduced speed near the end to prevent flash, improving product quality.
IV. Holding Pressure
Role of Holding Pressure and Time: Holding pressure compensates for shrinkage during cooling, and time determines its duration. Inadequate pressure/time causes surface sink marks, while excessive settings lead to internal stress and deformation. Holding pressure is usually ≤ injection pressure, adjusted by mold and material conditions.
Effect on Dimensional Accuracy: Proper holding pressure enhances product density and dimensional accuracy, crucial for high-precision items like optical lenses.
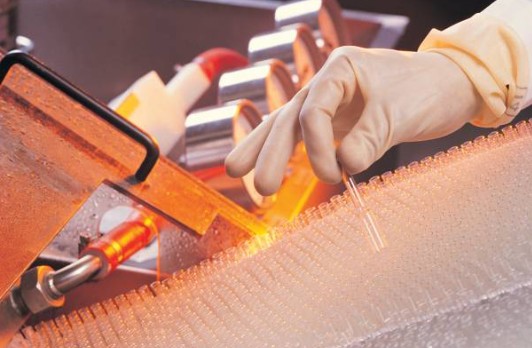
V. Screw Parameters
Diameter and L/D Ratio: Larger screw diameters suit large products, while smaller ones enable precise injection for small parts. A higher L/D ratio improves plasticizing but increases torque and energy consumption.
Rotation Speed and Back Pressure: Speed affects plasticizing efficiency but may degrade quality for heat-sensitive plastics. Back pressure improves melt quality; however, excessive back pressure reduces throughput. Minimal back pressure is preferred for quality assurance.
VI. Clamping Parameters
Clamping Force: It prevents mold opening during injection, related to cavity pressure and product projection area. Insufficient force causes flash, while excessive force damages the mold. Precision products require higher clamping force.
Opening Stroke and Plate Distance: The stroke determines product height, and plate distances define mold size compatibility. Improper settings affect product demolding and mold installation.
VII. Temperature Control
Barrel Temperature: Precision machines control barrel temperature within ±0.5℃. Deviations lead to inconsistent plasticizing and product defects. Different plastics have specific processing temperature ranges.
Mold Temperature: Controlled within ±1℃, it impacts filling, cooling, and product shrinkage. Crystalline plastics benefit from higher mold temperatures, while non-crystalline plastics prioritize flow and appearance.
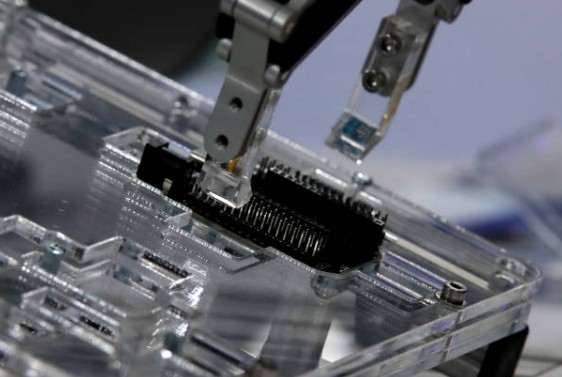
VIII. Other Key Parameters
Ejection Force and Stroke: Sized according to product characteristics, insufficient force/stroke fails demolding, while excessive values cause deformation.
Repeat Positioning Accuracy: Precision machines maintain position accuracy (e.g., injection ≤0.03mm) to ensure product consistency. High-precision sensors and control systems enhance accuracy.
Conclusion
All parameters of precision injection molding machines are interrelated and vital for the molding process and product quality. In practice, optimizing these parameters based on material, product, and mold characteristics maximizes machine performance. Technological advancements continue to improve parameter control precision and automation, offering new opportunities for precision manufacturing.
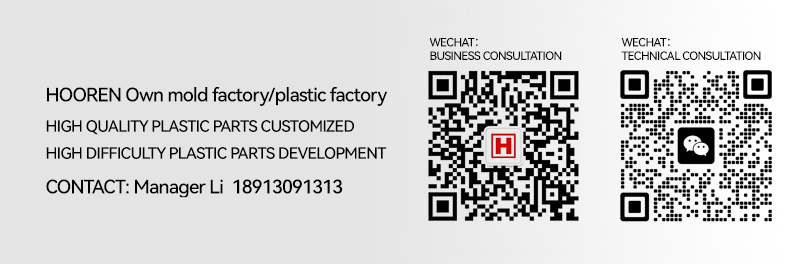