The reasons for the formation of shrinkage holes in injection molded parts are rather complex, mainly involving materials, molds, processes, etc. The following is a specific analysis:
Insufficient Injection Pressure: Injection pressure is an important driving force for the plastic melt to fill the cavity. If the injection pressure is not enough, the plastic melt cannot fully fill the cavity, and shrinkage holes will be formed due to volume shrinkage during the cooling process. Especially for some injection molded parts with complex structures and large sizes, sufficient injection pressure is required to ensure complete cavity filling.
Too Short Holding Pressure Time: The function of the holding pressure stage is to continuously replenish plastics during the cooling and shrinkage of the plastic melt to compensate for the volume reduction caused by shrinkage. If the holding pressure time is too short, the plastic melt will not be sufficiently replenished during the cooling process, and shrinkage holes are likely to be formed inside the plastic part.
Too High Melt Temperature: Excessively high melt temperature will reduce the viscosity of plastics and increase fluidity. After filling the cavity, the volume change is large during cooling and shrinkage, making shrinkage holes prone to occur. At the same time, high temperature may also lead to the degradation of plastic molecular chains, affecting the performance and quality of plastic parts.
Too Short Cooling Time: Insufficient cooling time means that the internal heat of the plastic part cannot be fully dissipated. After demolding, it will continue to cool and shrink, resulting in shrinkage holes. Moreover, too short cooling time will also affect the dimensional stability and mechanical properties of plastic parts.
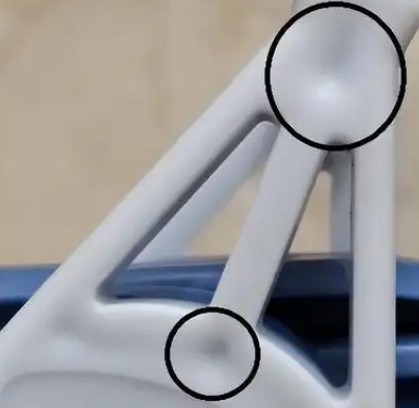